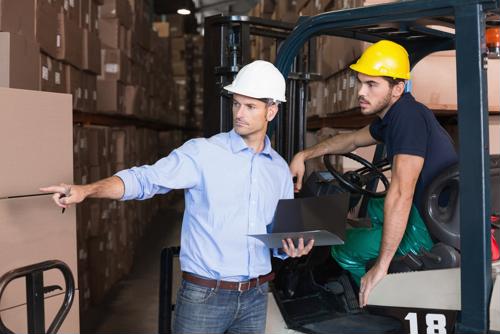
Forklifts are one of the most commonly used tools at industrial and commercial work sites. Their versatility and power make these machines a popular choice in a variety of warehouses, factories and production plants. However, forklifts also pose a variety of safety risks that are due not to any design or operational flaw, but simply their prevalence throughout the working world.
Developing an effective forklift safety program is critical to keep employees who work on and around these vehicles healthy and injury free. Let’s look at some common concerns around safe operation of forklifts, and how businesses can make positive changes to help employees use forklifts as safely as possible.
“There are nearly 100,000 forklift accidents each year.”
Common safety issues surrounding forklifts
An easy way to contextualize the size of the problem of forklift-related injuries is to look at how many accidents involving these vehicles occur each year. Safety + Health Magazine highlighted data from the Washington State Department of Labor & Industry that said close to 100,000 injuries involving forklifts happen each year nationally. Specifically, 62,000 nonserious injuries and 35,000 serious injuries related to forklift operation happen on a yearly basis. It’s clear that such injuries are unfortunately frequent and a major factor influencing a variety of workplaces.
According to OHS Online, the most prevalent fatal accident caused by forklifts is crushing injuries caused by a tipping vehicle. A variety of other incidents, from struck-by injuries to falls from these machines and workers being run over, can all cause serious consequences, up to and including death.
How can employers combat the many minor and major incidents that are possible when workers use these powered vehicles? Plenty of elements go into a comprehensive forklift safety strategy, and a few foundational components must be present to realize success:
- Effective training: Without a comprehensive program in place to educate staff, it’s nearly impossible to meet OSHA standards and avoid accidents. As Safety + Health magazine said, committing to safety involves investing in proper training that covers all pertinent areas of forklift safety. That means covering proper procedure to avoid the most serious types of injuries, such as properly balancing loads to avoid forklifts tipping over. However, a truly effective approach also requires reviewing the practices that can help employees avoid more minor incidents, including proper form for disembarking from these vehicles to avoid slip-and-fall accidents. This kind of approach requires employees to go through a full accounting of forklift safety.
- Strict limits for access: It’s clear that only trained, authorized personnel should operate forklifts, regardless of the specific situation. However, workers too eager to finish a job or trying to combat an unexpected absence can quickly put themselves and their colleagues at substantial risk for serious injury. Employers need to emphasize strong, consistently applied rules for using forklifts and establish meaningful consequences for unauthorized use.
- Vehicle and facility familiarity: In addition to the basic elements of safe operation, forklift operators should also have a deep understanding of all areas where they operate these vehicles. They also need to recognize any differences between individual forklifts in an employer’s fleet. Awareness of high-traffic corridors near where forklifts operate, tight corners and different weight limits for loads between machines are all vital for continued safe operation. Operators should regularly inspect their forklifts for any potential issues, and workplace safety managers should take a similar approach to reviewing how these machines operate throughout a facility.
Effective forklift safety practices are a cornerstone of keeping employees healthy and facilities operational. Turn to Total Safety to protect your staff, assets and work sites from a wide variety of operational health and safety concerns.