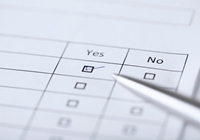
Chemical manufacturers keep up their health and safety programs to ensure workers are safe from incidents, but they may not know their initiatives are based on outdated information. When employers do not know about new regulations to control workplace hazards, there is a higher chance of injuries and incidents. Employers can better understand all of the risks of managing a chemical manufacturing facility by ramping up the number of safety assessments.
Companies often wait to conduct their safety assessments at the end of the year to allow employers to review past incidents and come up with safety measures to protect against recurrence. However, this approach does not help companies address urgent compliance or industrial hygiene requirements. To more effectively assess workplaces, employers should conduct evaluations more than once a year, according to an article published in the Journal of Business and Psychology.
Researchers suggest employers perform assessments at least once every three months."
How Often Employers Should Assess Workplaces
The U.S. Bureau of Labor Statistics reported there were more than 4,600 fatalities and almost three million workers had serious injuries in 2011. Considering the high chance of injury or fatalities, employers should review their work place to determine whether they have a strong safety climate.
The Journal of Business and Psychology study defines safety climate as the perception of the policies, procedures and practices connected to occupational safety.
When employees believe their workplace is safe, they often increase productivity. However, the perception of safety could change based on how companies analyze their safety procedures and potential occupational risks. Researchers suggest there is an expiration date for safety climate assessments resulting from the risk of outdated information.
Since annual safety checks are not enough to prevent injuries effectively, researchers suggest that employers perform assessments at least once every three months.
"Our results show that for the most critical relationship – predicting more severe incidents by safety climate – organizations should deploy safety climate surveys at least quarterly if not monthly," reported the Journal of Business and Psychology. "Further, we have outlined numerous ways that a safety climate assessment can expire, because conditions in the organization have changed."
Tips to Improve Safety Assessments
A successful safety assessment should be focused on hazard prevention and control. The U.S. Occupational Safety and Health Administration provides a worksheet for safety assessments that looks for the following:
- The presence of hazard controls. Employers should ensure engineering controls exist for specific hazards in the workplace, such as air purification solutions and gas detection systems to identify and control sources of potentially harmful gases and fumes.
- A plan for maintaining facilities and equipment. In addition to controlling occupational risks, companies should also establish a maintenance schedule that is important for hazard prevention. Employers should regularly maintain equipment, engineering controls and safety tools to minimize risks.
- Procedures and a team for emergencies. When there is an incident, employers should prepare the workforce for reacting to emergencies. To fully prepare for emergencies, workers should be trained in emergency response and understand their responsibilities in case accidents arise.