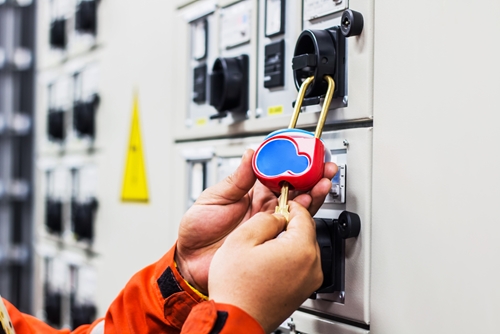
An effective lockout/tagout program is a foundational element of a larger health and safety initiative. The wide-ranging need to protect employees from the dangers posed by the unexpected operation of machinery presumed to be shut down for maintenance, repair or other service means many businesses have to develop effective LOTO procedures.
What makes a LOTO program effective, and how can companies develop rules that take industry changes into account in an agile, responsive way? Consider these pieces of advice:
Use modern technology to your advantage
“Making a few straightforward changes can significantly enhance employee safety outcomes.”
Physical training materials and reference sheets will always be useful in certain situations, but the rapid development of mobile technology means safety managers and other leaders need to look beyond hard copies. As Todd Grover, Master Lock senior manager, pointed out in an article for EHS Today access to information is one of the core issues involved in the complete implementation and correct use of a lockout/tagout program.
When a database of proper procedures is developed and made easily available to employees, the results are very positive. Entering a machine ID number or similar code into a mobile app’s search function is all that’s needed to find the specific, correct lockout/tagout process and have those directions available throughout the task. This simple and fast method for accessing relevant information boosts compliance efforts and means workers are less likely to make rough guesses about the proper approach or otherwise not fully follow the specific procedure needed to secure a specific piece of equipment.
Prudent use of technology makes developing and implementing a LOTO program easier, centralizing information and increasing ease of access. Incorporating the advantages of mobile devices and many other available assets makes compliance an effort more in line with many other business processes and the daily lives of many workers.
Make training efforts work for your business
Employees – whether they simply need to understand the restrictions on machine use relevant to a LOTO program or perform maintenance and lockout and tagout machines themselves – require effective training. This necessary effort shouldn’t be seen as a burden by safety managers, however.
A focused and productive training program encourages a high degree of compliance by providing workers with information about the reasoning behind a LOTO program, as well as the practical guidance for abiding by its rules. When employees understand why LOTO efforts are so important and how they benefit by following the rules, it’s easier to reach a high degree of adherence.
OHS Online highlighted the Occupational Safety and Health Administration’s regulatory requirement for annual LOTO training and advised businesses to look at that level of frequency as a baseline, not a level of high achievement. More frequent trainings allow safety professionals to focus on specific aspects of LOTO standards and develop a deeper understanding of them among workers. Other considerations, like ensuring multilingual training is available for employees with limited English proficiency, are vital to make educational efforts as effective as possible.
Improving a LOTO program doesn’t have to be a complicated or involved task. Making a few straightforward changes can significantly enhance employee safety outcomes.