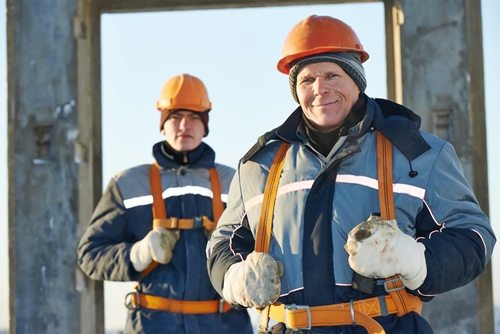
With the potential for extreme temperature changes outdoors, industrial workers need to be prepared to dress for protection against the elements during winter. Since the cold weather increases the possibility of hand injuries, employers should plan to protect workers' hands from winter-related safety problems.
Here are five tips to improve hand safety for the winter:
1. Choose PPE That Will Withstand the Cold
With exposure to the cold, industrial workers may be at risk for injuries to their hands, which makes personal protective equipment, such as gloves, necessary to work, especially outdoors. Provide workers with PPE that is made for freezing conditions to prevent frostbite and other health issues due to cold. These gloves could include linings made from warm materials that are wind and water-proof.
"Winter gloves should act as an extra layer of protection for employees and this means having PPE that fits the specific measurements of individual employees."
2. Size Gloves Properly
Although this tip may seem obvious, having gloves that fit correctly and guard against specific industrial safety hazards is essential to worker health and safety all-year round. Winter gloves should act as an extra layer of protection for employees and this means having PPE that fits the specific measurements of individual employees. Rather than using gloves that are one-size fits all, order gloves from manufacturers in a variety of sizes to ensure workers have the right fit and will cover their hands completely.
3. Select Hand Tools for Winter-Specific Gloves
With gloves on, employees might also need to make sure they will be able to handle tools properly. Test winter gloves when operating hand tools to see whether workers are comfortable. Having the right hand tools could prevent workers from putting their wrists in awkward positions, which could result in wrist and hand injuries, according to organization Choose Hand Safety.
4. Recognize Symptoms of Cold Stress
As an important step to maintaining worker safety, employers should train employees to be aware of the symptoms of frostbite and other signs of cold stress. Frostbite is usually exhibited when workers report reduced blood flow to their hands as well as numbness or tingling. Recognizing cold stress symptoms could allow workers to know when to take a break from working outside in the cold to avert winter-related hand injuries.
5. Be Prepared for Emergency Response
In case a worker has signs of frostbite or other health issues from the cold, employers should have medical equipment and supplies on stand by to help employees suffering from these symptoms. Supplies can include blankets and warm liquids to increase workers' body temperature after being outside, according to the National Institute for Occupational Safety and Health.