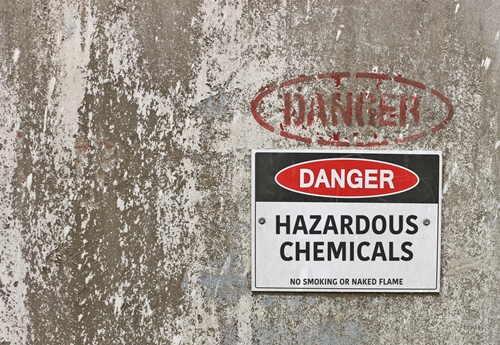
Eyewash stations and emergency showers protect one of the most sensitive and vulnerable parts of employees’ bodies when something goes wrong. Having these stations in place is critical to keep workers safe and to comply with the relevant Occupational Safety and Health Administration standards related to them.
OSHA’s rules for eyewash stations were first developed soon after the federal regulator was created in 1970. The organization called for immediate access to suitable stations for rinsing both eyes and the rest of the body when employees could come into contact with injurious, corrosive materials. As Occupational Health & Safety magazine pointed out, OSHA’s definition of these materials centers on the ability of the agent to destroy or irrevocably alter the structure of the bodily tissue contacted after the exposure occurs.

Getting ANSI involved
While OSHA makes it clear that any employees who may be exposed to chemicals or other dangerous substances meeting the specified criteria have access to eyewash stations and emergency showers, it doesn’t define the nature of those precautions. Companies had to deal with about a decade of time where OSHA mandated the inclusion of these emergency safety tools but did not provide broad guidance beyond configuration or installation, excepting quick access for affected employees.
For a clear, visible and roundly accepted method of determining the suitability of eyewashes and showers, a large number of organizations have turned to the American National Standards Institute’s Z358.1 Eyewash and Shower Equipment Standard, OH&S magazine said. That industrial safety standard covers many specifics of eyewash station and shower function, as well as certification and testing, maintenance of equipment and employee training for proper use.
Some major considerations
The ANSI standard allows for both fixed stations and portable ones. Fix stations tend to use potable water as a flushing agent, which is acceptable under the relevant standards and regulations but creates the potential for significant issues as compared to a saline solution or specially treated water. Tap water isn’t meant to be placed in direct contact with the human eye for extended periods of time, and can cause secondary problems.
“Tap water does not have the composition of human tears,” Dr. Henry Edelhauser, director of Ophthalmic Research at the Emory University School of Medicine, told OH&S magazine. “Tears are a naturally buffered, salt solution. Tap water is not buffered, nor does it contain any of the necessary salts.”
As EHS Today pointed out, fixed stations using potable water require regular maintenance to remove any potential contamination from particulate or chemicals. The website highlighted an instance of a technical safety specialist inspecting an eyewash unit and finding a lack of care had caused the water to resemble chocolate milk as flowed out from the station. That potential lack of maintenance is serious and could cause substantial issues for any employees who rush to use such a unit following accidental exposure, up to and including potential loss of vision.
Additionally, placement has to be a priority. The ANSI standard sets the maximum time an employee should have to spend between exposure and reaching the station at 10 seconds. This time element is foundational in the effectiveness of any eyewash station or emergency shower.