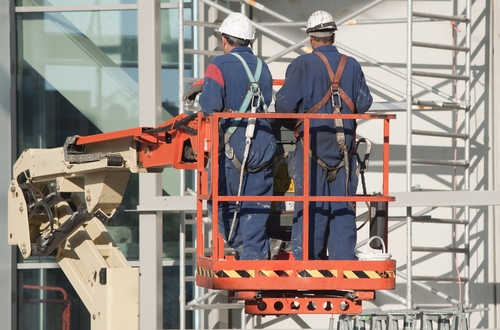
Fall protection is a common concern for a wide variety of businesses, from contractors to manufacturers and distributors. Employees regularly need to work at potentially dangerous heights to deal with tasks ranging from equipment assembly to facility maintenance. Having an effective fall protection plan is critical, especially considering how common these incidents are.
The Occupational Safety and Health Administration (OSHA) ranked violations related to fall protection the most common infraction seen by its inspectors in both 2015 and 2016. In the longer term, issues with fall prevention have regularly ranked on OSHA’s top 10 list for many years. The high incidence of accidents related to a lack of adequate fall protection means businesses need to emphasize this aspect of their overall safety plan.
Improving fall protection efforts
“Companies have to regularly evaluate their fall protection efforts.”
As part of the regular development of a safety plan, businesses survey new facilities and take a variety of potential hazards into consideration. This includes fall protection, and the construction or move-in phase offers an opportunity to minimize the work employees do at unsafe heights – defined as four feet above ground level for general industry – as well as implement effective fall arrest systems.
Companies can’t stop there, however. They also have to regularly assess the facility and the condition of any measures used to protect employees from falls, like toe boards and handrails. Additionally, assessing any new additions or changes to previous workflows should be a priority. A minor change to the way an employee completes a task could be significantly more efficient overall but also increase the risk of a fall, something that needs to be addressed with the appropriate personal protective equipment or more permanent alterations to the environment.
Inspections also need to address fixed hazards and the resources used to guard employees from harm. Holes large enough for employees to fall into, for example, require a railing and toeboard or floor hole cover. Hazards below the four-foot mark that pose a risk related to a fall – where tripping would bring a worker into contact with dangerous machinery or substances – needs to have fall protection in place as well.
Employee training is another critical consideration, and one that also has to be regularly revisited. The need for comprehensive training, which stretches from describing the hazards of falls and how improper use of fall protection systems can increase the risk of employees suffering an injury to proper equipment inspection and maintenance, is ongoing. New employees need to be trained before they take on any tasks at dangerous heights, and refreshers for existing employees can go a long way toward making sure they stay as safe as possible.
Fall protection involves a lot of moving parts and a regular commitment to training staff and inspecting work areas, but this type of proactive stance will keep your workers safe and your facilities in accordance with OSHA’s fall protection regulations.