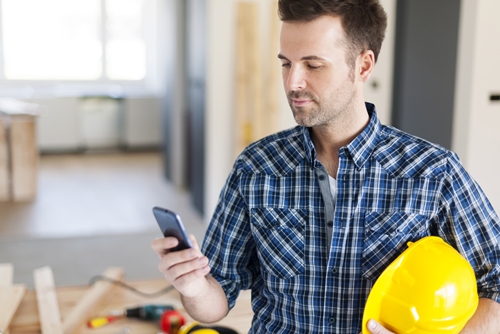
There are an untold number of ways technology has been created and modified to improve worker safety. Innovation has truly made some dangerous workplace situations safer.
As worker safety continues to remain on the mind of employers, one piece of technology seeks to provide even more safety for employees.
The power of Bluetooth
If you own one of the newest smartphones, you've likely heard of Bluetooth. Essentially, these devices, when Bluetooth is enabled, transmit information over short length radio waves, according to the Bluetooth organization. TechTarget says, when Bluetooth is enabled, devices interconnect wirelessly. It was first introduced in 1994 and interestingly enough, one company does not own the technology. Instead, some of the world's leading device manufacturers formed the Bluetooth Special Interest Group. They work together to advance the technology and ensure all users stay informed of the latest updates.
In recent years, Bluetooth has become synonymous with connecting wireless headphones to smartphones. The same concept applies to the workforce, but on a much larger scale.
Lose the cables
At the consumer and industry level, Bluetooth-enabled devices are appealing because wires are seldom involved, according to Sensear. This detail therefore eliminates potential safety hazards. For example, if you have an employee who wears ear protection, he or she will not have to worry about wires tangling or getting caught on small objects.
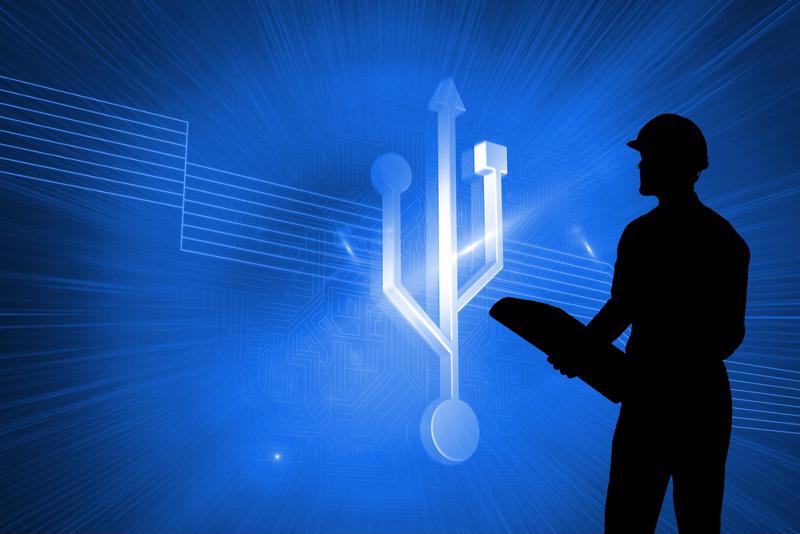
Monitor employee's safety
One of greatest aspects of Bluetooth is its potential. The technology is constantly being upgraded and offers employers numerous radio profiles, Sensear noted. Device manufacturers have taken advantage of the potential and have created tools to monitor employee safety. Product offerings from Motorola and Blackline Safety help protect workers, no matter what industry they're working in.
However, to combine Bluetooth and safety, employers have to understand what difficulties workers are facing. For instance, construction companies may lose precious time while waiting for employees to check in the office, only to then make their way to the job site. Using various Bluetooth products, employees can be tracked in a safe, secure and private manner. This therefore eliminates the check-in process as managers can easily account for their workers.
As another example, Bluetooth can monitor employees' safety. The wide appeal of Bluetooth is recognized by the ability to install it on numerous devices, such as mobile phones and Motorola's MOTOTRBO radios. According to SEI Wireless Solutions, Bluetooth can be combined with specific software to send workers "Alive Check" messages. If the worker responds without issue, there is no harm. It's even designed to automatically keep track of important metrics. This system, like others, are appealing because of the flexibility offered and because Bluetooth is readily available on so many devices.
Impact on industries
Incorporating Bluetooth technology into the workplace is an excellent way to monitor the safety and well-being of employees. It is low cost, energy efficient and works well with personal and work-issued devices. Instead of relying on phone calls for check-ups, employers can utilize Bluetooth to remotely and wirelessly ensure everyone is safe.