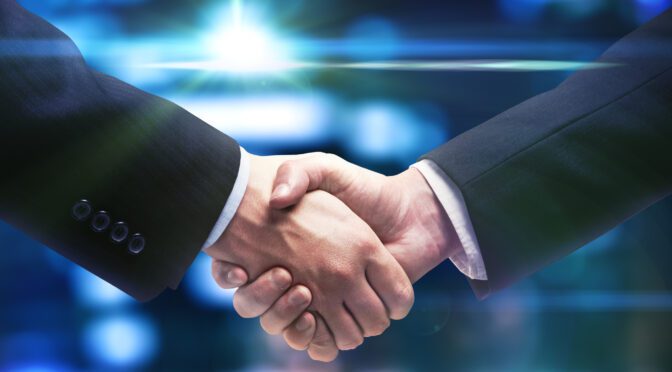
HOUSTON, September 13, 2019 (Newswire) – Total Safety, the world’s leading provider of integrated safety technologies and services, announced today that it has acquired S&S Supplies and Solutions to expand its distribution offerings providing customers with safe, reliable industrial products and safety supplies through best in class distribution solutions. S&S has a network of distribution centers strategically located in key industrial markets throughout the US and is a leading supplier of safety products, industrial supplies and related compliance services to the power utility, automotive, airline and energy end markets. Total Safety will organize around two separate business units, Industrial Safety Services and Specialty Distribution, which will operate S&S independently under the S&S brand.
“S&S provides us with an immediate capability of delivering safety products, industrial supplies, and solutions to our customers across the U.S. and soon throughout the world,” said George Ristevski, CEO. “It gives us access to distribution capabilities into a broader group of customers, particularly the power utility end market. We are committed to offering a complete set of safety solutions that drive safety, productivity and reliability for our customers. Our expansion into specialty distribution will supplement our technical safety services with industrial supplies, safety products and supply chain solutions providing turnkey services for all our customers’ safety and reliability needs,” said Ristevski.
“Total Safety is the right strategic partner for S&S having similar values and objectives in serving our customers,” said Tracy Tomkovicz, CEO, S&S. “We are particularly excited about sharing our respective and complementary capabilities to better service our customers and to help Total Safety expand into the power utility market,” said Steve Tomkovicz, President, S&S. Both Tracy and Steve will remain in their leadership roles and will focus on implementing Total Safety’s distribution strategy.
About Total Safety:
Total Safety is the leading global provider of integrated industrial safety services, equipment and compliance solutions, providing safety equipment, technology and data that make a meaningful difference in the way businesses run. Based in Houston, Texas and operating from 200 locations in more than 20 countries, our nearly 3,600 employees help our customers increase employee health and safety, meet compliance and regulatory requirements, boost productivity and reduce downtime. Driven by our unwavering commitment to our mission …to ensure the safe Wellbeing of Workers Worldwide® we work across all sectors, including oil and gas, petrochemical and refining, utilities, manufacturing, construction and mining. Visit us at www.totalsafety.com to learn more.