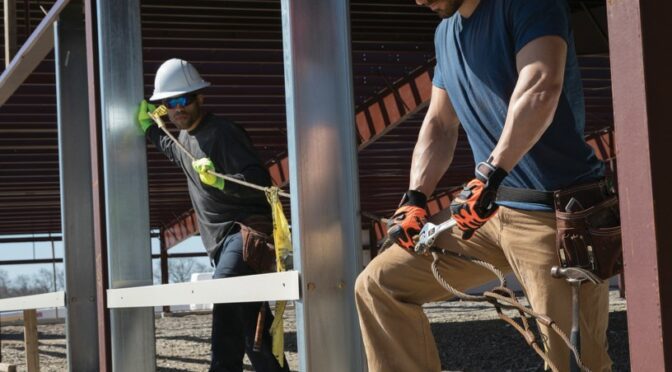
Excessive heat is a threat to the safety of workers — especially those working outside in construction, oil and gas, agriculture and similar industries. If their bodies cannot release heat as quickly as it accumulates, workers can face numerous health risks, such as fatigue, fainting, cardiovascular issues, impaired judgment and other symptoms of heat related illness.
One critical consideration for outdoor workers in the summer is head protection. In fact, according to recent Honeywell studies, the color of a plastic hard hat is directly related to the heat affecting the body. This guide explains three key steps to help safety managers choose the right hard hats to protect outdoor workers in the hottest months of the year. (Information from Honeywell)
1. ASSESS THE HEAT RISK
According to the Occupational Safety and Health Administration (OSHA), temperatures as low as 71° F can still be dangerous for workers engaged in heavy exertion. That’s because ambient air temperature — the reading on a thermometer — does not tell the entire story of heat risk. Other contributing factors include direct sunlight, relative humidity, and radiant heat reflected from water, windows or metal structures.
Therefore, in assessing the heat danger for outdoor workers, keep in mind that even though the ambient temperature may seem comfortable, workers could still be at risk.
How does it really feel outside? The answer is reflected in the Heat Index, which combines relative humidity with the actual air temperature. Consider this guide from the National Weather Service. Download the NIOSH/OSHA Heat App [iOS | Android] to access a simple heat calculator on your device.
2. CHOOSE LIGHT-COLORED HARD HATS
All hard hats reflect, absorb and transmit some infrared rays from the sun.The rays that are absorbed through the shell become trapped, increasing the temperature of the air gap surrounding the worker’s head. There are a variety of factors increasing the temperature of the air gap, including the angle of the sun, the amount of wind, the ambient temperature and the color of the hard hat.
Honeywell tested the impact of color on the temperature that the worker is subjected to. We put identical hard hats of different colors on head forms inside a controlled environment that was tuned to resemble a warm summer day. The hard hats were then exposed to an infrared heat lamp to simulate the sun. Thermocouples were placed on the outside of the hard hat shell and inside the shell, just above the head form. Honeywell found that in a 90° F environment, the temperature of the air gap beneath the hard hat shell (the air that the worker is actually exposed to) ranged from 111.6° F to 122.3° F.
In fact, Honeywell found that depending on the color, the outer shell of a hardhat can become 60 degrees warmer than the ambient temperature, while the temperature inside the hard hat can become more than 30 degrees warmer than the ambient temperature. Clearly, selecting light-colored hard hat in warm temperature conditions can make an enormous difference in a worker’s health and safety.
How does the color of a hard hat contribute to heat risk? Honeywell studies show that in a 90° F environment, the temperature surrounding a worker’s head is lowest with hard hats that are white and highest with hard hats that are orange or high-visibility yellow.
Honeywell replicated these results by setting up several hard hats on head forms in warm, sunny environments across the globe. The sunlight-powered experiments provided data that was consistent with our controlled tests.
In summary, the head form under the light-colored hard hats was significantly cooler than under darker colored hard hats. Interestingly, the orange color performed the worst, allowing infrared rays to penetrate the shell and creating the highest temperature in the air gap surrounding the worker’s head. White compared favorably to all other colors, making it the ideal hard-hat color to help mitigate heat risk. Across the spectrum, a good way to improve worker safety in the heat is to swap out darker hard hats for lighter colors.
3. CHOOSE UNVENTED HATS
Adding vents to hard hats should lower the temperature underneath, right? Not so. Venting creates a window for sunlight to seep into the hat, which means higher temperatures for the worker’s head. Moreover, vented hats do not have enough room to allow air to flow properly, unless the air enters the vent on a strong wind — and even then, the cooling effect is only momentary. Therefore, vented hard hats generally do more harm than good.
How to select the right hard hat for hot conditions. Hard hats of different colors can be important indicators of job roles on a worksite, enabling quick identification of key people. But for jobs in direct sunlight, lighter-colored hard hats can significantly reduce the risk of heat stress and improve workers’ safety. Download full article from Honeywell
To select hard hats for hot conditions, please contact your Total Safety sales representative. Total Safety helps organizations achieve higher safety standards and create a workplace culture of safety. Go beyond the basics with our VMI solutions, high-quality safety equipment, PPE, and MRO solutions. We are committed to helping you meet compliance, reduce injury, and help to protect the safe well-being of your workforce.
W³…to ensure the safe Wellbeing of Workers Worldwide. ®
Full article by Honeywell and re-posted by Total Safety. Download study here.