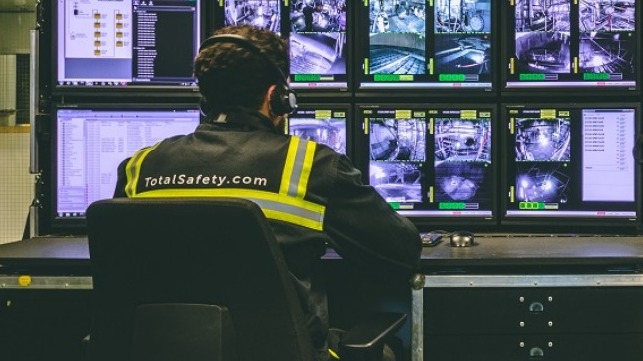
Mark Barker is the Senior Vice President of Total Safety and has worked in industrial safety for 36 years. Check out his guest post on Maritime Executive HERE.
Please upgrade to Microsoft Edge, Firefox or Chrome for optimized website viewing.
Mark Barker is the Senior Vice President of Total Safety and has worked in industrial safety for 36 years. Check out his guest post on Maritime Executive HERE.
There are unique challenges oil and gas companies must face when it comes to working with hazardous chemicals. Gases like hydrogen sulfide naturally occur during extraction operations, which make it a common risk for workers in the field.
Working in an enclosed environment that may contain hydrogen sulfide combines two occupational safety hazards: confined spaces and hazardous gas exposure. With the risk of exposure to highly toxic gases like hydrogen sulfide, employers need to safeguard workers using gas detection equipment.
Here are reminders of the steps needed to ensure compliance regarding confined spaces:
Use gas detection
As part of the U.S. Occupational Safety and Health Administration’s rules, companies should monitor enclosed spaces for gases before allowing workers to step into these areas. Enclosed spaces can include tanks, silos and other places where it is difficult for employees to enter and exit. Employers could install gas detection machines to measure the level of air contaminants. Proper air monitoring is an OSHA requirement for confined spaces that need permits because of the potential presence of atmospheric hazards.
Companies could use single-gas monitors or multi-gas monitors to ensure hazardous gases are not present in enclosed spaces before oil and gas workers enter these confined areas. OSHA requires that employers perform continuous gas monitoring.
Be aware of the symptoms of gas exposure
Employees should recognize the symptoms of chemical exposure, such as when they encounter hydrogen sulfide gas. These signs may include coughing and shortness of breath in the case of low concentrations of exposure. Although hydrogen sulfide has a distinct smell, workers may not be able to immediately tell how much exposure there is without devices like gas detectors. Devices such as these should accurately measure and report the level of hazardous gas in the area.
Establish a line of communication
Another precaution employers should take is to make sure they have a colleague or manager outside the enclosed space. Having someone on the outside and maintaining a line of communication either through verbal commands, keeping personnel in their line of sight or using electronic devices could prepare them for any emergency or rescue services in case hazards are detected.
Use respirators
In the event employees are at risk for exposure to dangerous gases, employers should provide workers with personal protective equipment such as respirators that will prevent inhalation of gases and their negative health effects.
There are pieces of equipment unique to the oil and gas industry that need proper machine guarding. Workers in the sector are at risk for crushing injuries and amputations that could be caused by moving parts or malfunctioning machinery.
According to the U.S. Bureau of Labor Statistics, the oil and gas industry had 112 fatal occupational injuries and 1,400 nonfatal injuries and illnesses in 2011.
Oil and gas staff may be at risk for losing their fingers, limbs or other incidents if companies do not protect employees by using machine guards and training them to be aware of workplace hazards.
Assess Machine Functions and Risks
To determine whether equipment requires machine guarding, managers should go around the workplace and assess them for specific risks. These can include moving parts that could result in workers being struck or crushed. They can also make note of what is considered a safe distance to prevent someone being pulled in or struck by machinery.
What Parts Should be Guarded?
With machine guarding, managers should determine whether they should guard against components such as rotating equipment like belts or gears, as well as parts that could impact or draw workers in. These include abrasive wheels that should be guarded based on the type of the wheel and work being performed.
“Companies should inspect machines for any signs of damage that could indicate that machines are not safe to operate.”
Inspect Machine for Damage
While some machines are inherently dangerous, machines that have been ill-maintained or not inspected in a long period of time may put workers’ safety at risk. Companies should inspect machines for any signs of damage that could indicate machines are not safe to operate. Operate the machines and see whether they are defective or malfunctioning to see whether they need maintenance or should be pulled out of the workplace.
Train Workers on Machine Guarding and Recognizing Hazards
Workplaces with machine guards should also make sure workers understand the importance of these safety devices as well as how they work, according to the U.S. Occupational Safety and Health Administration. Managers should train employees to recognize specific hazards with machines and educate them on the right way to operate machinery. Employees should be reminded to avoid equipment that do not have guards. They should also know to alert managers to any problems with the guards or the machines themselves to address the issue quickly and safely.
When workers have to perform duties within confined spaces, they will likely be their colleagues’ sight. This could result in increased risk to their personal safety if they cannot be seen and there is an issue with the space, such as the presence of hazardous gas.
Since these spaces are not designed for continuous occupancy or have restricted means for workers to exit and enter through, there are risks with enclosed areas that could require immediate attention if workers are in danger, the U.S. Occupational Safety and Health Administration notes.
“While the risks within confined spaces are not readily apparent, workers should continuously monitor these areas for any buildup of gas and vapors that could cause occupational fatalities.”
Fatal injuries associated with confined spaces reached their highest level in 2000 with 100, according to an analysis of data from the U.S. Department of Labor’s Bureau of Labor Statistics Census of Fatal Occupational Injuries (CFOI) program. Fatalities in enclosed areas is a significant problem for the upstream oil and gas companies. Since then, upstream deaths in the oil and gas industry have fluctuated with 15 recorded in 2012, down from more than 40 in the previous year, according to OSHA data.
While the risks within confined spaces are not readily apparent, workers should continuously monitor these areas for any buildup of gas and vapors that could cause occupational fatalities.
With the risk of worker deaths in confined spaces, staff should be prepared to go into these areas with knowledge of proper communication procedures and equipment, including:
Use walkie talkies
As workers may not be able to see each other if one is inside in a confined space and the other is outside, a direction line of communication using walkie talkies, or other two-way radio devices will help maintain contact even if supervisors cannot keep them in their line of sight, according to OSHA. Using two-way radios can alert the staff member outside of the enclosed space if someone is in need of rescue or emergency medical services in case things go wrong. Other communications equipment can include cellphones, however, the conditions of an enclosed space may make it difficult for phones to receive a signal.
Monitor confined spaces with cameras
While co-workers may not be able to see their colleagues while they are in a confined space, advanced camera monitoring technology could do this job for them. Using cameras could give managers or other workers the eyes they need in and out of a confined space to gauge the safety status of people in these areas.
Total Safety, the world’s leading provider of integrated safety services and solutions, announced today that it has acquired Pivotal Safety, a full-service safety company serving Western Canada. This acquisition enhances Total Safety’s geographic footprint in Western Canada, and will allow the combined company to bring to bear a broader offering of safety solutions and technologies to serve its customers across Canada.
“Canada is an important market for us and with the addition of Pivotal to our operations, our ability to serve our customer base has dramatically improved in the Canadian market,” said George Ristevski, Total Safety CEO. “We are excited to partner with Pivotal Safety’s talented management team to embark on the next phase of growth for Total Safety in Canada. The combination of our businesses allows us to provide a wide range of safety services, technologies and highly experienced safety professionals to address our customers’ needs.”
Glenn Roberts, former President of Pivotal Safety, will lead the combined company’s Canadian business unit and will assume the role of Vice President, Total Safety Canada. “Total Safety is an ideal strategic fit for us—our two companies share a common vision and mission, as well as a commitment to superior execution for our customers. We look forward to joining Total Safety and leveraging their scale to continue our growth in the Canadian market,” said Mr. Roberts.
About Total Safety:
Total Safety is the leading global provider of integrated industrial safety services, equipment and compliance solutions, providing safety equipment, technology and data that make a meaningful difference in the way businesses run. Based in Houston, Texas and operating from 176 locations in more than 20 countries, we help companies increase employee health and safety, meet compliance and regulatory requirements, boost productivity and reduce downtime. Driven by our unwavering commitment to our mission …to ensure the safe Wellbeing of Workers Worldwide,SM we work across all sectors, including oil and gas, petrochemical and refining, utilities, manufacturing, construction and mining. Visit us at www.totalsafety.com to learn more.
ENQUIRIES:
Media Contact:
Paul Tyree
281-867-2303
ptyree@totalsafety.com
Total Safety, the world’s leading provider of integrated safety services, announced today that it has strengthened its Canadian presence by acquiring Vantage Safety Services. Based in Clairmont, Alberta, Vantage Safety Services is a full-service industrial safety company providing services to all segments of the oil and gas industry.
This acquisition continues Total Safety’s expansion and commitment to the Canadian market. It expands the company’s presence in the Grande Prairie area and provides increased service to customers in Northern Alberta and British Columbia. Vantage Safety Services will be integrated into Total Safety’s Canadian operations.
“We continue to focus on high quality acquisitions that further establish Total Safety as the leading global provider of integrated safety services and technologies,” said George Ristevski, Total Safety CEO. “Vantage Safety’s success in Grand Prairie will allow us to strengthen our service capabilities.”
“We are excited to be a part of Total Safety and look forward to better serving our customers with our combined capabilities, said Todd & Shirley McKeever, founders and principal executives at Vantage Safety. “Total Safety has a customer and employee centric culture that will fit well with our company.”
Total Safety also announced yesterday that it has acquired Pivotal Safety based in Bonnyville, Alberta.
About Total Safety:
Total Safety is the leading global provider of integrated industrial safety services, equipment and compliance solutions, providing safety equipment, technology and data that make a meaningful difference in the way businesses run. Based in Houston, Texas and operating from 176 locations in more than 20 countries, we help companies increase employee health and safety, meet compliance and regulatory requirements, boost productivity and reduce downtime. Driven by our unwavering commitment to our mission …to ensure the safe Wellbeing of Workers Worldwide,SM we work across all sectors, including oil and gas, petrochemical and refining, utilities, manufacturing, construction and mining. Visit us at www.totalsafety.com to learn more.
ENQUIRIES:
Media Contact:
Paul Tyree
281-867-2303
ptyree@totalsafety.com
Fall protection is an enduring concern for everyone from individual employees to safety managers and business leaders. Fall protection often appears on the Occupational Safety and Health Administration’s list of top 10 most common violations and related training requirements, reaching No. 9 on the most recent list. How can your organization effectively address fall protection training to keep employees safe and productive while avoiding regulatory complications?
OSHA made a variety of rule changes related to fall protection that were finalized in 2017 and have already or will soon become enforceable. An effective fall protection training program has to take the latest regulatory developments into account.
The rule changes don’t all require more stringent monitoring or additional restrictions, either. An update to the walking-working surfaces rule means businesses can make more choices related to fall protection systems, finding the ones that offer the best fit for their employees. The one restriction, pointed out by For Construction Pros, is personal fall arrest systems can no longer incorporate body belts. The rule also emphasizes the need for training related to fall hazards and fall protection systems, a vital consideration for developing effective educational offerings for workers.
Other rule updates include:
Effective training ultimately means workers understand all the critical elements of fall protection. From how to properly apply personal and collective fall protective equipment to identifying potential hazards and inspecting work areas, there are many needs that must be addressed.
OSHA already requires that a competent person lead the educational efforts for staff. Depending on the specific circumstances of your facility, you may want to consider having veteran workers with strong safety records involved in certain aspects of training. Whether it’s teaching best practices for ensuring PFPE is correctly applied or pointing out potentially dangerous areas of the facility or worksite where employees have to carry out tasks at heights, these experienced employees can contribute both directly and indirectly.
Some veteran staff hold fall protection in a high regard and are fastidious in terms of their approach to safety. Others may develop less-positive habits over time if they don’t experience any accidents and eventually come to believe their experience is more important than the best practices for safety, pointed out OHS Online.
Safety managers and business leaders need to recognize that training compliance is important for staff members old and new. Although experienced employees have more knowledge of existing conditions and established safety workflows, refreshers on those topics are always a positive in terms of overall workplace safety. Additionally, employees of all types are in the same boat when it comes to learning about new types of PFPE and CPE, changes to the workplace, regulatory developments from OSHA and other changes. Effective, compliant training has to include all workers.
Make sure your training efforts are supported by the best fall protection equipment possible. Get in touch with Total Safety today.
The financial repercussions of a lack of safety and environmental controls in the oil and gas industry can’t be overlooked. For the Sunoco Pipeline, which recently resumed construction in Pennsylvania following a total shutdown and substantial fine, the absence of oversight had significant negative impacts on the project’s completion and its total cost.
The pipeline is intended to move natural gas across Pennsylvania, with a western termination point in eastern Ohio and an eastern one near the state border with Delaware. As with other projects of a similar scope, construction of the pipeline required a variety of permits and other permissions to ensure it complied with a wide range of state environmental and workplace laws. A documented lack of compliance led to Pennsylvania’s Department of Environmental Protection rescinding permits until the company building the pipeline fixed the relevant issues. The builder had to pay a fine of more than $12 million and remediate a host of issues related to construction before it was authorized to continue.
The specific problems presented by the construction included a series of spills and leaks of drilling fluid, as well as a variety of other violations noted as egregious and willful by the state DEP, according to the Associated Press. DEP officials made a point of noting that the violations represented a clear problem and said the agency would only reverse its position once all of the issues related to construction were addressed.
The project eventually resumed following a consent order and agreement that included the $12.6 million fine and extensive revisions to the operations plan used for the rest of the construction, Occupational Health & Safety reported. The changes included a renewed commitment to follow established protocols contained in the original plan as well as additional protections and safeguards to ensure a high degree of safety for surrounding towns and the environment.
“Throughout the life of this project, DEP has consistently held this operator to the highest standard possible,” DEP Secretary Patrick McDonnell said, according to Occupational Health & Safety. “A permit suspension is one of the most significant penalties DEP can levy. Our action to suspend the permits associated with this project, and the collection of this penalty, are indicative of the strict oversight that DEP has consistently exercised over this project. Today’s announcement is by no means the end of DEP’s oversight.”
The stoppage spanned a little more than a month, from early January through early February, and is a critical reminder of the need for a high degree of compliance from the very beginning of an oil and natural gas project through its entire useful life. Workplace safety and compliance issues take on new, much broader boundaries when the worksite stretches across an entire state. To make sure your projects are as safe and compliant as possible, get in touch with Total Safety today.
New hires are a vital part of every business and every industry. The need to replace employees who retire, leave for new opportunities or otherwise depart may be constant or occasional, but a new worker is almost always needed to ensure things continue to go smoothly.
Of course, a new hire has to be brought up to speed on how an organization operates and there’s nothing more important than ensuring they can work safely to keep themselves, their coworkers and the facility as a whole safe.
“Research found new hires are significantly more prone to injury than long-term employees.”
The vast majority of businesses already have new hire training for both operational and safety considerations in place. That doesn’t mean those processes don’t need regular review, however, nor that they might need to be tweaked or even overhauled from time to time. How can your facility make sure it addresses new hire safety concerns in the most effective way possible? Consider these foundational concerns:
It’s important to remember that new hires have a different perspective than veteran workers and can be more predisposed toward accidents. Research from the Institute for Work & Health, shared by Safety + Health magazine, said workers in their first month at a new employer have more than triple the risk of an injury that results in time away from the position compared to someone who has been in the same position for more than a year.
“We can only speculate on the ‘why,'” said Curtis Breslin, an IWH scientist who participated in the new hire research. “One thing studies have shown is that there’s a lack of familiarity. That’s a common theme that could be contributing to new workers’ increased risk. The other possibility is that new workers might be encountering more hazards. Or their risk perception – they don’t have the knowledge and awareness, so they’re underestimating the risks. It could be issues with training, maybe they’re not being trained [on or receiving] on-the-job, hard-knocks-type training that happens in the first or second month.”
Although every workplace is different, addressing new hire safety is a common goal. Keeping employees safe and active on the job is a benefit for everyone involved. To address the unique aspects of educating these inexperienced workers and preventing any harm, keep these strategies in mind:
A recent fatal gas well explosion in Oklahoma is an important reminder of the need for constant vigilance in terms of workplace safety, especially when it comes to potentially dangerous materials, equipment and operations. Although the vast majority of wells operate safely and without incident, the stakes are especially high for workers and businesses when something goes wrong. Let’s look at the details of this accident and the issues that may have led to it.
“The accident is a powerful reminder of the need for effective workplace safety planning.”
The Houston Chronicle called the incident the deadliest accident related to the oil and gas industry since the Deepwater Horizon explosion in 2010. That catastrophic failure resulted in 11 deaths and 17 injuries at the offshore platform, affecting a significant percentage of the 100-plus crew members on site. The Oklahoma incident involved a massive explosion that led to five deaths as well as an assortment of injuries in Quinton, a small city in the southeast quarter of the state.
Issues related to extinguishing the fires ignited by the explosion meant emergency responders worked from Jan. 22, when the incident occurred, through the next day before they could fully control the situation. The status of the deceased workers wasn’t confirmed until that point.
Local NBC affiliate KJRH reported on the findings of the Chemical Safety Board so far in its investigation of the incident, which began shortly after the explosion. The federal workplace safety watchdog is still looking into the exact circumstances that triggered the fatal accident, although it has determined that the crew working on the well rig had removed the drillpipe and other, related tools from the well as they began to change out the bit used on the drill. The companies involved in staffing and operating the well have cooperated fully with the CSB’s work, and agents will continue to interview eye witnesses and examine the damaged worksite in an effort to determine exactly what occurred.
The drilling segment of the oil and natural gas industry is more prone to accidents than many others. Jim Wicklund, a Credit Suisse analyst who works with the industry, reminded the Chronicle that several rigs are lost each year to accidents and explosions, although he also pointed out that fatalities are rare. How can businesses, from executive leaders to safety managers and on-site specialists, emphasize keeping workers safe in an especially dangerous circumstances?
A quick survey is a good place to start. Employees should be able to answer many of the questions in Energy HQ’s “How well do you know oil and natural gas safety?” quiz, and safety specialists should have no trouble answering most, if not all, of them. Identifying gaps in knowledge among frontline workers and safety professionals can help steer efforts for education and training toward the specific areas where they’re most needed.
Creating a greater sense of community and mutual importance around safety training can also have a positive impact. Oil and gas well workers have tough jobs with long hours, but they also need to effectively interact with parts of an expensive, complicated and potentially dangerous piece of equipment as they work. This common situation can be leveraged in group training that allows time for relationship building within crews, which can easily lead to a more active and attentive attitude about the safety of coworkers.
Investing in the right safety equipment is also a critical component of preventing accidents. Total Safety is here to help businesses involved in all phases of oil and natural gas production and transport operate as safely as possible.